Panther Cannabis Nanoemulsification Equipment
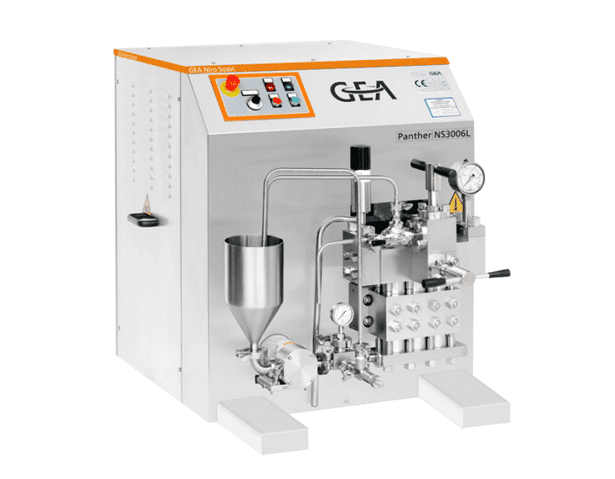
TECHNICAL DATA
Model | Panther 1200 | Panther 1500 |
---|---|---|
Max Flow Rate | 100 L/h | 50 L/h |
Production Rate (10 mg servings/h) | 100k (flavorless) | 42k (flavorless) 200k (high-load) |
Pressure | 1,200 bar | 1,500 bar |
Motor Power | 5.5 kW | |
Electrical Options | 3Φ 200 V, 50 Hz 3Φ 220 V, 50-60 Hz 3Φ 400 V, 50 Hz 3Φ 460 V, 60 Hz | |
Required Utilities | Lubricating and cooling water – 60 L/h | |
Feeding Hopper Volume | 4.5 L | |
Minimum Sample Volume | 200 mL | 120 mL |
Dimensions (LxWxH) | 1255 x 885 x 1180 mm | |
Weight | 560 kg |
Optional Upgrades Include:
– Heat Exchanger for product outlet
– In-Line Medium SS Tank System (1-6 gal)
– In-Line Large SS Tank System (1-12 gal)
Key Features
- Flow rates up to 100 L/h, produces up to 680k 10 mg servings per 8-hour shift
- Produces water-soluble cannabinoid nanoemulsions that are easily added to beverages, edibles and topicals
- Benefits include enhanced shelf-life, improved bioavailability, and faster uptake
- Clean-In-Place (CIP) and simple preventative maintenance procedures
- More precise dosage due to true homogeneous mixing
- Produces clear, high-load, or flavorless nanoemulsions with Root Sciences’ proprietary formulations
- Proven homogenization technology used in beverage, chemical, and pharmaceutical processing
Advantages of Products Manufactured with Nanoemulsions
Hemp and cannabis nanoemulsion-based products provide
substantial benefits compared to traditionally manufactured
edibles and beverages.
The proprietary nano emulsification and micronization
technologies greatly increase the bioavailability of
cannabinoids. This creates a substantially more stable
product that is highly resistant to separation. Products
created with nanoemulsions take effect more quickly than
traditional infused edibles and deliver more consistent and
enjoyable experiences for consumers.

High-Pressure Homogenization
Nanoemulsions are stable dispersions of two immiscible liquids, such as cannabis oil and water. The tiny droplets of oil are typically between 20 and 600 nanometers in diameter and are stabilized by a thin film of surfactants.
First, a coarse emulsion with large droplet sizes is created through the use of a high shear mixer. Then the coarse emulsion is passed through a GEA High Pressure Homogenizer several times. This process can easily be integrated into a large scale manufacturing line.
The GEA pressurizes the fluid and then releases it through a special homogenizing valve. The extreme shearing forces the emulsion experiences during this process causes the droplets to become extraordinarily small, improving its stability and bioavailability.
GEA has been at the leading edge of homogenization technologies since 1947, servicing the food and dairy, pharmaceutical, chemical, and biotechnology industries. GEA produces the worlds largest high pressure homogenizers, with flow rates of up to 5,000 liters per hour at 1,500 bar.
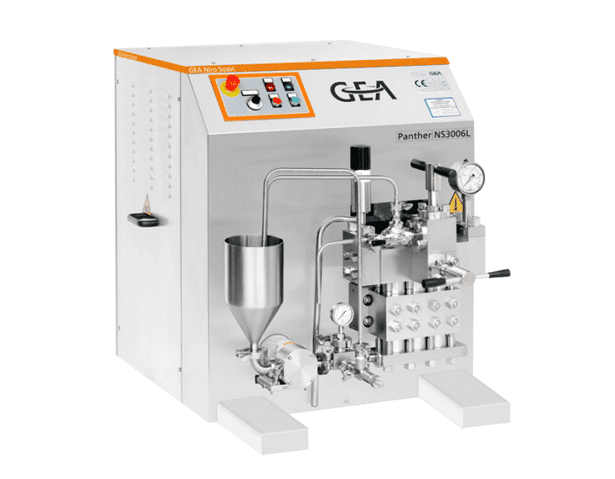